Aris Syntetos, Dan Eyers: PARC Institute of Manufacturing, Logistics and Inventory,
Cardiff Business School, Cardiff University
Executive summary
Many commentators have lamented global supply chains for exacerbating the problems of COVID-19. In principle, there may be some merit in their argument. Indeed, there have been notable examples where global supply chains have failed, creating significant negative consequences. The supply of PPE (Personal Protective Equipment) is just one glaring example and other operations that are reliant on responsive delivery (e.g., Just-in-time operations) have faltered, disrupting operations and restricting supply to customers across the world. Even before the pandemic, there was an increased emphasis on the transition from extended supply chains that stretched across continents to supply chains that are more regionalised and local and hence shorter. Advances in technology - AI, IoT, additive manufacturing, Industry 4.0 and the digital revolution have all been heralded as enablers to make supply chains more dynamic, flexible and transparent. As well as the technological enablers, governments have promoted the benefits of near-shoring and reshoring as a means to protect economies and create jobs. Such policies are seen as obvious means to re-juvenate battered economies after the pandemic.
However, aside from adopting protectionist approaches to the balance of trade, the obvious logic is that geographically shorter supply chains are inherently less susceptible to risk. De-risking the supply chain and maintaining the continuity of supply has become more of a priority over the last decade. Natural disasters have disrupted supply chains, trade tariffs have become more widespread and the rise in e-commerce trading have all impacted supply chain design and decisions. The growth of e-commerce has put a different dynamic on supply chains, with consumer expectations driving increased focus on rapid fulfilment and delivery. The pandemic has accelerated the growth in e-commerce over and above this already upward trending business model.
The future focus to build back better and the demand to make future supply chains environmentally sustainable has also increased scrutiny on the long, elongated take-make-dispose supply chains common today. With consumers and even previously reticent governments acting with more urgency to address environmental issues, sustainability has risen on organisational agendas.
This study aims to explore whether COVID-19 will lead to a shift in future global supply chains. Recognising that every influencing factor or impact upon supply chains would cover a broad spectrum, we decided to undertake our exploration by revisiting the interface between supply chains and disaster management. This is particularly important because, unlike other disasters, COVID-19 is geographically unconstrained and attacks all three pillars of sustainability (economic, societal, environmental) simultaneously.
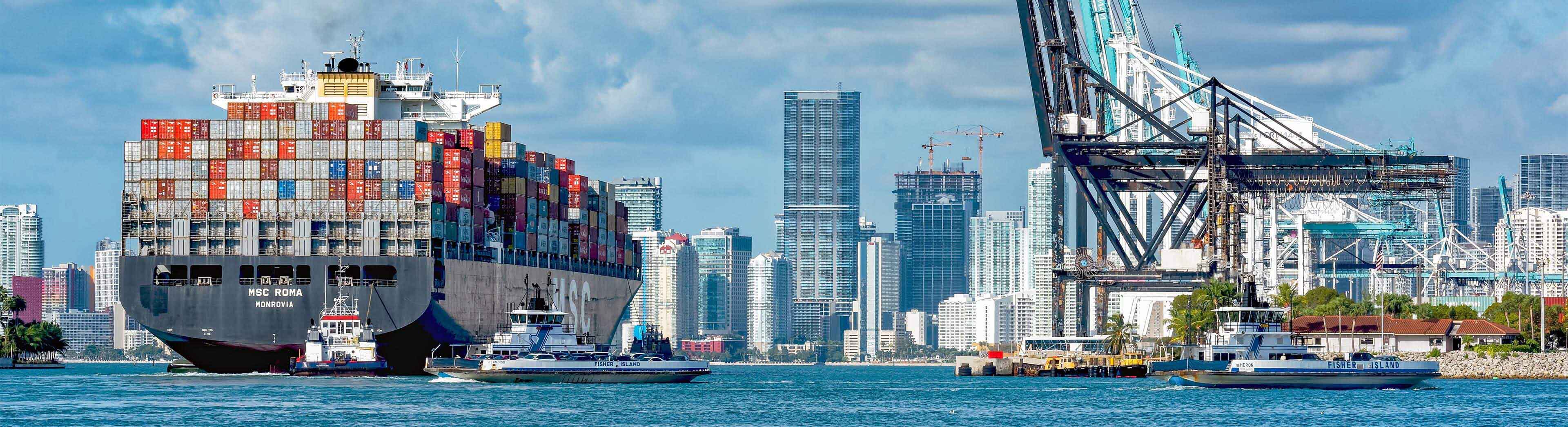
Unsurprisingly, we find that there is no one magic answer, no single approach that works across every supply chains. It is a heavily nuanced problem that requires careful management to balance risk with operational efficiency. Our research highlights benefits related to the localisation of production. At the same time we find supply chain managers are placing emphasis on blended strategies to ensure some of the economic benefits of global sourcing are not compromised. Furthermore, we find strong enthusiasm for the movement from single- to multi-sourcing, spreading the sourcing risk with multiple suppliers. Additionally, we find much emphasis on the effective management of logistics, particularly in the extended supply chain. Our work shows that relationships between partners in the supply chain are crucial, and that having established relationships pays real dividends in times of crisis. Based on the result of this study, we provide a matrix to support decision making for managing strategic supply chain decisions, allowing firms to intelligently identify opportunities that achieve maximum benefits and manage risks.
What’s the Challenge?
As the backbone of modern businesses, supply chains are an integral part of globalisation. How companies’ source, manufacture, deliver, and return goods has evolved greatly over time. Enabled by a plethora of technological developments, global supply chains have never been more complex – but at the same time, they have never been more efficient. As the complexity and challenges of extended global networks rise, some shifts in supply chain design have already been witnessed. The recent pandemic has highlighted the urgency of evaluating the implications of supply chain designs and has forced companies to accelerate decision making on future supply chain design and execution.
There have always been disasters, and mankind has always had to deal with them. In recent decades companies have learnt to confront shocks triggered by manmade disruptions and natural disasters. The concept of 3R (resilient, robust, and responsive) supply chains is already well established (see, e.g., Purvis et al., 2016; Spiegler et al., 2012), but COVID-19 has put this concept to the test. The evidence is that many supply chains have not passed the test.
Since COVID-19 emerged, the world has witnessed stringent government measures including lockdowns and travel restrictions, to slow down the spread of the virus. As a result, and due to the COVID-19-induced economic shocks, the world’s GDP has declined dramatically. An early report by Accenture in March 2020 (Accenture, 2020) suggests that 94% of Fortune 1000 companies had already experienced disruptions triggered by COVID-19, with 75% of them having been negatively affected. Take the aviation industry as an example; based on data from the International Civil Aviation Organisation, the estimated airline revenue loss for 2020 approached $400bn (ICAO, 2020).
COVID-19 has revealed the fragility and weakness of global supply chains – how vulnerable established networks can be to unforeseen disaster-induced shocks. Unlike other disasters though, what we currently experience is geographically unconstrained and deeply hurts all aspects of sustainability. Indeed, some authors argue that when combined with existing political and environmental headwinds, COVID-19 may deal a fatal blow to global supply chains.
The current situation might be an excellent opportunity for companies to review their set-up and strategies to build better supply chains. In this work, we explore the interface between supply chains and disaster management to understand how firms can create robust supply chains to withstand disasters, but without compromising the efficiencies that make them competitive in a global marketplace. We focus on the four key stages of disaster management – Preparation, Response, Recovery, Mitigation / Prevention – and explore how leading companies are approaching this challenge. Valuable lessons emerge from this exercise to prepare companies for the post-coronavirus economy.
What’s the background?
The COVID-19 pandemic is often termed as an ‘unprecedented’ disaster, and certainly the scale and magnitude eclipse most events in recent memory. Worldwide, about 120 million people have been infected and at least 2.6 million people have lost their lives (at the time of writing; WHO, 2021). In response, for over 100 countries worldwide, there has been some degree of lockdown, disrupting flows of both people and goods. The economies of many countries have entered an economic recession; for some, this has become a depression.
Despite the scale of the COVID-19 disaster, it does share the generic attributes that can be assigned to all other disasters:
- Preparedness: Being ready and having plans in place to cope with a disaster.
- Response: The enactment of plans to respond to the disaster as it unfolds.
- Recovery: Focusing on the short and longer-term restoration of normality.
- Mitigation and/or prevention: Putting measures in place to prevent the disaster from reoccurring, or at least lessening its impact.
The mitigation and prevention of future emergencies are obviously of exceptional importance, and the humanitarian aspects of such emergencies are broadly defined to include all human, material, economic, and environmental impacts. Such impacts (and their moderation/prevention) heavily depend on the organisation of the corresponding (material, resource, financial, information and human) flows. It comes as no surprise then that the area of disaster supply chain management and humanitarian logistics has attracted considerable attention in both academic and practitioner literature. In Figure 1 we show what is known as the Disaster Life Cycle (or Emergency Response Cycle).
Disasters are low-frequency incidents and are very hard to predict and manage (Nikolopoulos, 2021), thus making it difficult to justify why resources should be devoted to proactively manage such risks (Altay and Ramirez, 2010). If a risk never materialises, the expenses incurred on risk assessment and preparedness are hard to justify to top management (Zsidisin et al., 2000). In 2003, it was reported that despite the risks, 95 percent of Fortune 500 companies were not equipped to manage a disruption that the company had not experienced before (Mitroff and Alpaslan, 2003). However, compelling evidence has been accumulated over the last 15 years or so, to suggest that poor disaster management may have devastating consequences for society and the economy (see, e.g., Sodhi, 2016).
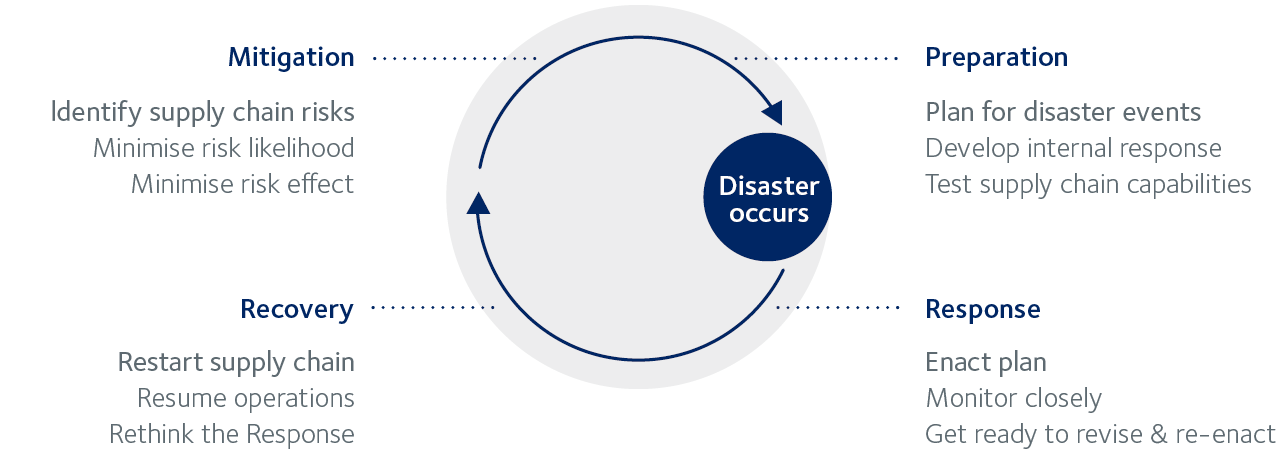
Supply chains have been increasingly designed with resilience, robustness, and responsiveness (3R) in mind to mitigate the tremendous impact that disasters often have. The (estimated) financial damage caused by reported natural disasters is increasing (see Figure 2) , and naturally so does the attention that the 3Rs receive and their importance for our economy.
However, previous research has shown that different kinds of disasters have different impacts on societies and economies, therefore arguing against an all-hazards approach (Altay and Ramirez, 2010) suggested by the Federal Emergency Management Agency (FEMA). Further, and unlike other disasters, COVID-19 has been geographically unconstrained and its impact (which is ongoing at the time of writing) is unparalleled to what we have previously observed. It seems important then to understand in some more detail the nature of such impact, and the response to it, in order to guide supply chain professionals on how to adapt their supply chains for the long term.
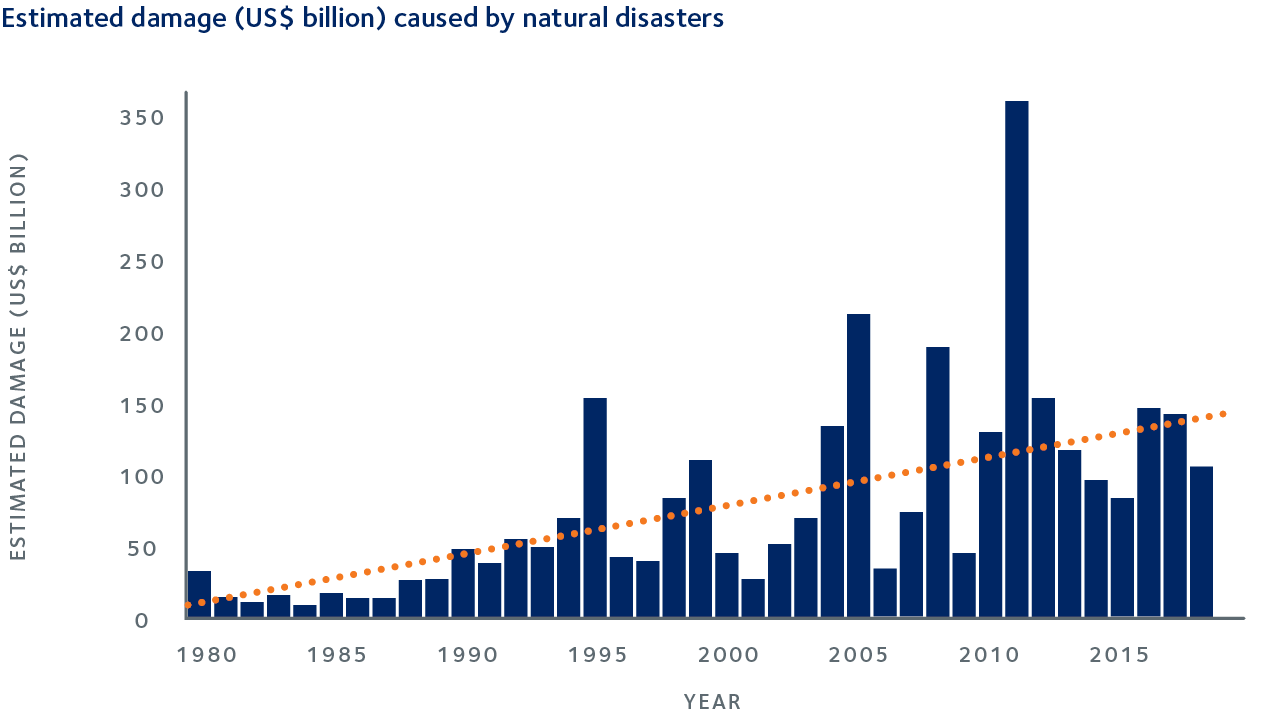
Method
We employed an exploratory approach towards the data collection and analysis undertaken in this study. Semi-structured interviews were conducted with senior managers from ten organisations, enquiring about the immediate impact of COVID-19 on supply chains, and expected changes that will be made in future because of these experiences.
The preparation of the interview instrument and the entire research process were conducted in accordance with Cardiff University’s research ethics protocols and approved by the relevant committees. The interviews were organised around the four stages of disaster management (Preparation, Response, Recovery, Mitigation/Prevention). The companies come from various industries such as telecoms, medical, electronics and technology industries and examples of responding companies are Brother International, Nokia, Inmarsat, Signify.
The interviews were transcribed, followed by a thematic coding of the data using a qualitative data analysis software (NVivo). Such software allows the opportunity to group qualitative information and facilitates the process of identifying key themes.
Subsequent discussions allowed key insights to emerge around the four stages of disaster management, and the development of a prescriptive decision-making matrix to support strategic supply chain decisions. The methodology we followed is summarised in Figure 3.
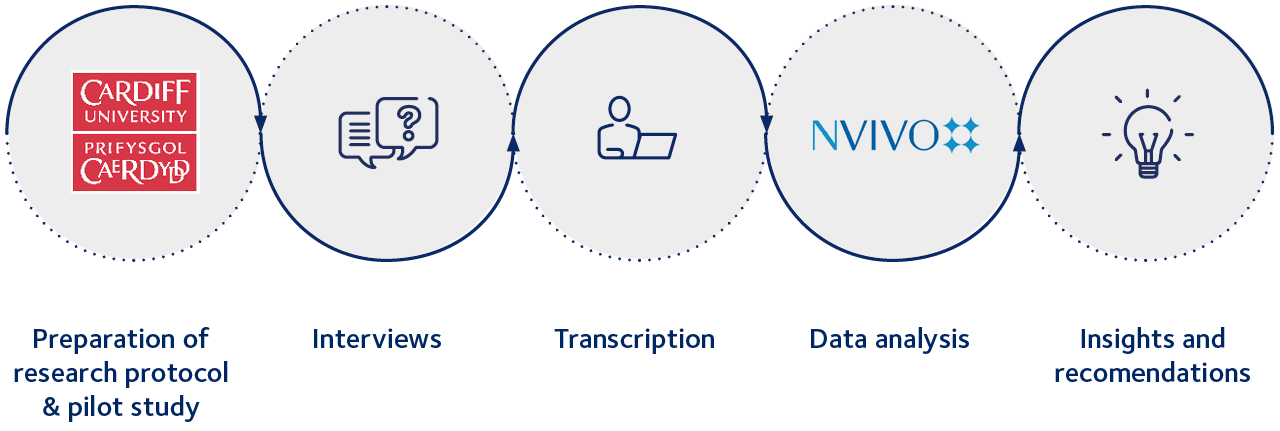
Discussion
What’s changed?
COVID-19 has had a tremendous effect on various supply chain aspects, and the companies interviewed collectively see these changes falling under the following categories: demand, organisation, people, production, sourcing, and transport.
Companies faced huge step changes in demand (both up and down, depending on the nature of the products), which in conjunction with the supply volatility led to service levels being severely impacted. Product portfolios had also to be revisited, as
“Certain parts of [the] our portfolio suddenly became extremely popular. For example, smaller printers that you can use at home. And some of our more corporate printers became less popular because nobody was actually in the office.”
-Supply chain manager, an electronics company.
Well established organisational abilities were criticised and proved to be ineffective. In particular, supplier communication channels that were previously believed to be productive failed, and the importance of information sharing mechanisms to allow responsiveness appeared to be key to make the right decisions as the crisis evolved. Continuity planning was also seen not to be working as expected. Companies did have various relevant plans in place but the fact that such plans could not be operationalised raised many questions. Finally, the pace of response was seen to be linked to making sure that
“We have a stable enough and extensive enough supply chain support from transportation companies so we can really choose the most optimal way on how to react fast.”
-Supply chain logistics operations director, a technology company.
With regards to people, protecting the employees and making the right staffing decisions (as to who is working where) were found to be extremely difficult to make, although ad hoc team collaboration initiatives were praised. Daily problem solving calls were employed in many cases to keep the communication together globally in much faster (than usual) time.
Production capabilities suffered invariably, and so did sourcing. Supply chain collaboration was commented upon as a key enabler of responsiveness and stability. Companies that work collaboratively with customers and suppliers tried to avoid the creation of the bullwhip effect (the phenomenon where order variability increases as the orders move upstream in the supply chain) by not passing upstream the surge in demand they faced from their customers, a surge that could be explained and analysed. Interestingly, in some companies, protectionism of national supply also seems to have emerged, whereas this was never the case before for these particular companies.
Finally, and with regards to transport, companies commented on the lack of capacity to move goods from one continent to another, though problems were also thought to be very much country-related, depending on how regulated the lockdowns were implemented. Once organisations realised that they were in low stock or in a back-o order situation, the availability of air freight – due to the combined effect of reduced capacity available and the additional demand from the amount of PPE being shipped predominantly from China – meant that finding space was a challenge. The extended delivery times for international transport and the increased costs were used to explain the, otherwise previously not present, focus on national supply chains.
What’s the effect of global supply chains?
All respondents agreed that involvement in global supply chains played an important role in the challenges (and opportunities) their organisations were faced with. Opinions seem to converge also with regards to ‘cheapest isn’t always the best’, because the cheapest rate does not get you the uplift you need in bad times! The main challenges/opportunities are summarised in Table 1.
Effects of global supply chains | Comments |
Supply chain fragility |
With one exception, all respondents agreed how unexpectedly fragile supply chains ended up being, and the sensitivity and complications induced by globally inter-connected supply chain networks. |
Supply restoration delayed |
Respondents argued that what companies will inevitably reflect on is the possibility of shortening some supply chains or, certainly having some supply chains that are country-specific. |
Airfreight capacity |
The world used to be heavily reliant on freight aircraft and you could get such space easily. This has been severely challenged. |
Changing contingency plans | Companies started with contingency in Asia, thinking that Europe and the US were still quite a safe place but then, of course, ended up with the same challenges everywhere. |
Draw on extra suppliers |
A global supplier base, in conjunction with close relationships, meant that the effect of COVID-19 was lessened. |
Increased importance of communication | COVID-19 amplified the need to get communications right and the need to manage physical part flows and customer orders. Companies introduced daily global operational calls to align seamlessly on a global scale. |
Production delays (and staff unavailability) | COVID-19 created a distinction between those employees who can work from home and those who are required on site to keep supply chains moving. Key employees who were not able (or willing) to get to work created delays for both supply, production, and delivery steps in the supply chain. |
Table 1. The effects of global supply chains
How well did we respond?
The respondents were asked to comment on how well (or not) their local supply centres (where they existed) responded to the COVID-19 changes. Although their responses highlighted the potential to be much better, local supply centres were predominantly perceived as positive, offering the respective organisations the opportunity to learn.
There was an appreciation of the circumstances, with organisations working with their suppliers to level the demand and informing them of the demand they were facing by their customers. Respondents argued that
“It was key to work with them [the suppliers] and work within their limitations, which allowed us to keep the continuity of supplies.”
-Purchasing manager, a medical company.
Global organisations with a presence in China and therefore experiencing the impact of the first wave of disruptions were credited with sharing lessons learned, whereas those organisations with European hubs and without the global network were criticised for not appreciating the difficulties soon enough.
(The information collected was not sufficient to examine country-level effects and respective organisational differences (for example, differences between Chinese and European operations), and in any case, such examination was not part of our research objectives.)
There was also a change in working practices, mainly manifested through the following:
- More variability in working hours across functions.
- The management of inventory. Initial problems of localised increases in inventory (due to imbalances between supply and demand) would eventually be seen to offer a competitive advantage.
- New policies to adapt to the impact of the virus: in terms of health and safety protocols, and relevant processes and procedures and close coordination of the above with 3PL companies.
- Prioritisation of work and orders, fulfilling those judged more critical.
- Sharing resources and experience, upstream and downstream within supply chains.
Localisation was predominantly associated with a positive effect, due to inherently closer relationships, shorter lead times and an increased degree of flexibility (or correspondingly a lower level of constraints). Nevertheless, it was also perceived as something practically difficult to achieve nowadays (due to long and complex supply chains), and blended strategies were advocated to ensure the economic benefits of global sourcing were not compromised.
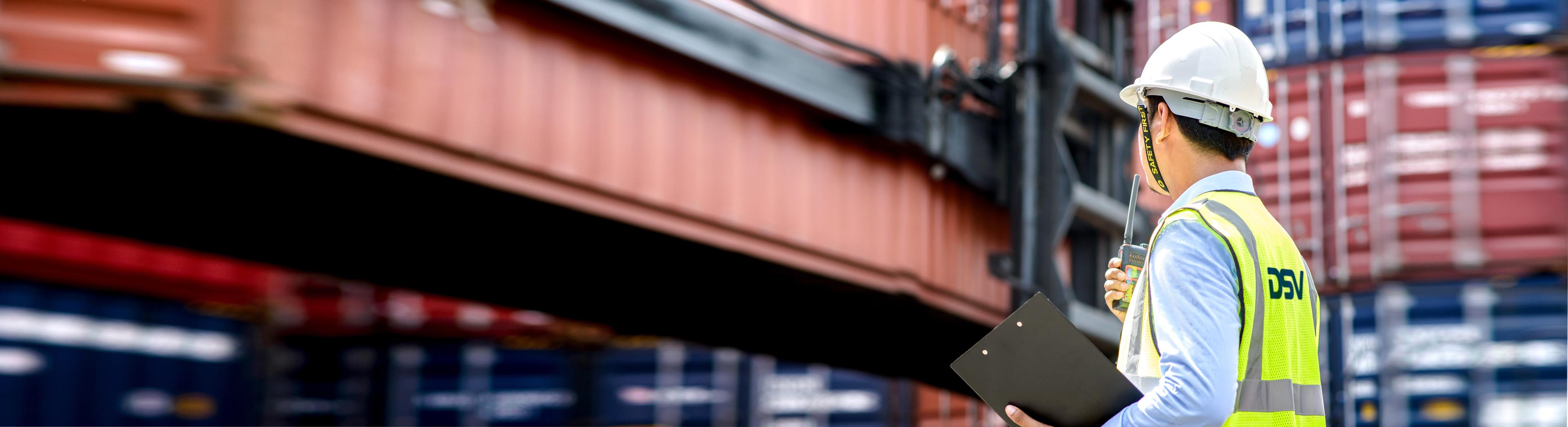
What’s the effect on future business?
Although one respondent mentioned that it is perhaps too early to comment on the effects of COVID-19 on future business, opinion amongst the rest of the respondents is divided.
Some do not envisage much change into the way they currently operate. Forecasting and inventory optimisation will continue to be regularly conducted, and the inter-play between local and regional inventories (and their use for supply chain needs) is something that many companies have recently been paying particular attention to. Further, European organisations were recently forced, because of Brexit, to revisit their contingency plans and conduct regular risk analysis. So, in that respect, some companies do not foresee any changes, over and above what was planned already, because of COVID-19.
In contrast, other companies foresee new strategies being developed, with regards to:
- Alternative sourcing plans.
- Inventory optimisation, both in terms of location (closer to customer) and quantities (being used as a mitigation mechanism).
- Production, in terms of introducing real time, smart, data-driven capabilities.
- Re-evaluating risk, in terms of re-assessing the viability of local arrangements previously thought to be non-economically desirable.
- Regional planning, in terms of managing risk mitigation through higher inventories or through localisation. It is important to mention that respondents foresee some increased nearshoring:
“We are already talking to our key suppliers about how we can have more local for local supply without crossing global regions.”
- Supply chain planning and control director, a telecoms company.
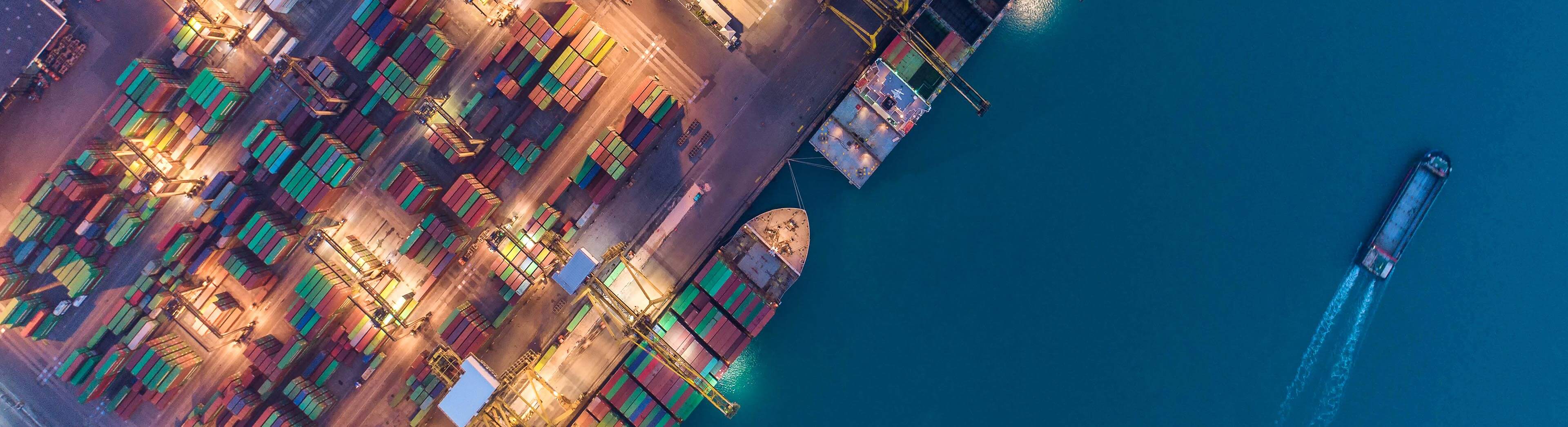
Does local supply promote robustness?
The respondents were asked to comment on whether a local supply base promotes robustness. As one respondent said: the devil is in the detail, and the answer depends on what sort of business we refer to and how the upstream and downstream supply chain looks like. So, for some of the respondents, the answer depends on: i) the degree of overall benefit; ii) the product itself.
Companies are increasingly receptive to the idea of manufacturing in multiple locations.
“But for a low margin product that you might have to manufacture in massive volumes to make it interesting, then whether you are going to be willing to do that [localise]….I am not sure.”
- Head of global distribution network, a telecoms company.
The complexity of the supply chain is also a key determinant of the right approach. In the electronics or FMCG (Fast Moving Consumer Goods) sector, for example, the reality is that whether we manufacture the products locally or not, the supply chain behind them will be long. So, and unless we refer to specific areas in China where the entire supply chain may be contained within a region, this is something difficult to achieve.
Other respondents supported the fact that local supply may not be associated with robustness arguing that: i) all supply chains are inherently global, ii) good relationships offset location, iii) is not financially sensible to opt for local rather than global, iv) things will recover anyway in the longer term, so the justification for local supply would only have a short-term emphasis.
Those in favour of local arrangements argue that it is all about balancing, and ‘seeing’ both, supply and demand, and local supply allows one to achieve this. Regional supply chains, whereby in each continent there are end-to-end capabilities to produce buffer and deliver may be the key to avoid disruption. Regionalisation has been argued to be the right strategy to mitigate pandemic-induced risks. Further, diversification strategies do not necessarily mean that one needs to go all local, but rather having contingency plans which are able to redirect certain critical component supplies from local suppliers (see also next section).
Does local supply promote resilience?
The respondents were also asked to comment on whether a local supply base is more resilient, i.e. able to overcome shocks, than an extended supply chain. The opinion was divided, with those arguing for, commenting on i) the reduced complexity and the opportunity for a quick efficient response; ii) the meaningfulness of such arrangement in particular industries, e.g. the food industry; and iii) the back-up opportunities being offered. Interestingly, global localisation or offering a local option but without being fully localised were repeatedly mentioned here.
“So, the diversification has to also relate to the fact that it does not mean it immediately has to go all local, but you need to have contingency plans which are able to redirect certain critical component supplies from local suppliers. This definitely has a benefit, but obviously it's also about the lead time and the cost combination, that has to be taken into account.”
- Supply chain logistics operations director, a technology company.
Those that argued against, supported this position with examples of European and worldwide suppliers reacting as well as local suppliers, and emphasising the importance of supplier relationships. The loss of economic competitiveness was also put forward as an important reason, focusing on economies of scale and cost minimisation. Local suppliers (where there is no ability to divert resource or supply) are perceived as more exposed to financial risk and had it not been for the global supply, companies would have experienced service failures.
“If our local supply chain were only in any one of those regions [Americas, Europe and APAC], we would have most likely seen a service outage to our customers.“
- Supply chain planning and control director, a telecoms company.
What is the future of global sourcing?
The last two questions posed to the respondents were an attempt to summarise thoughts and depict (in few words) the future of global sourcing. Although few argued that in the long term, and unless governments are involved, things will not change, most of the respondents envisage major changes, that may be categorised as follows:
- Increased focus on risk: companies will be increasingly looking at risk identification and mitigation
- Reduction in single-sourcing strategies: while supply chain managers have always assessed the trade-offs between single and dual/multiple sourcing scenarios, the respondents collectively argue that there will be a reduced reliance on China as a single source of manufacturing by introducing alternative sources of supply.
- Re-evaluation of importance (trade-offs) of low cost versus increased risk: the true cost of extended supply chains is to be reconsidered taking into account risk factors, and reliability of supply.
The future of manufacturers that will continue outsourcing their core activities to a location that is far from the market depends very much on several factors, like i) ‘appetite for risk’ and projected profit margins; ii) country capabilities (but even location capabilities within a country) and social impact; iii) ease of localising; iv) existing infrastructure and potential for regionalisation; v) supplier power dynamics and vi) trade agreements.
The above should be viewed in conjunction with technological developments and shifts that are also likely to determine decisions, perhaps to a greater extent than risk considerations do. Such technological changes do not refer only to manufacturing capabilities but also to third party logistics (3PL) service provision and particularly those 3PLs that have already embraced such challenges and evolved their service offerings. It can be argued that in the near future distinguishing between manufacturing and logistics will be a difficult thing to do, as the Internet of Things (IoT) blurs such boundaries. There will be things that make things, things that move things and things that do both. Of primary concern will be the coordination of such making, moving and doing and, in turn, the efficiency of integrated logistics manufacturing services.
Takeaway
It comes as no surprise that our primary data and analysis indicate there is not one right way forward. Instead, COVID-19 is prompting supply chain leaders to ask different questions of their supply chain and place emphasis on areas that in the past may have been overlooked, particularly supply chain risk.
Overall, it seems that companies need to reassess their capabilities to do what is needed, and recalibrate their supply chains to i) further exploit previously undermined strengths (e.g., close supplier relationships), and ii) rectify structural flaws inherited from old business models that have gone unquestioned for years (e.g., sourcing from suppliers solely based on cost).
The key findings of the interviews are reflected in a decision-making matrix to support strategic supply chain decisions (Figure 4).
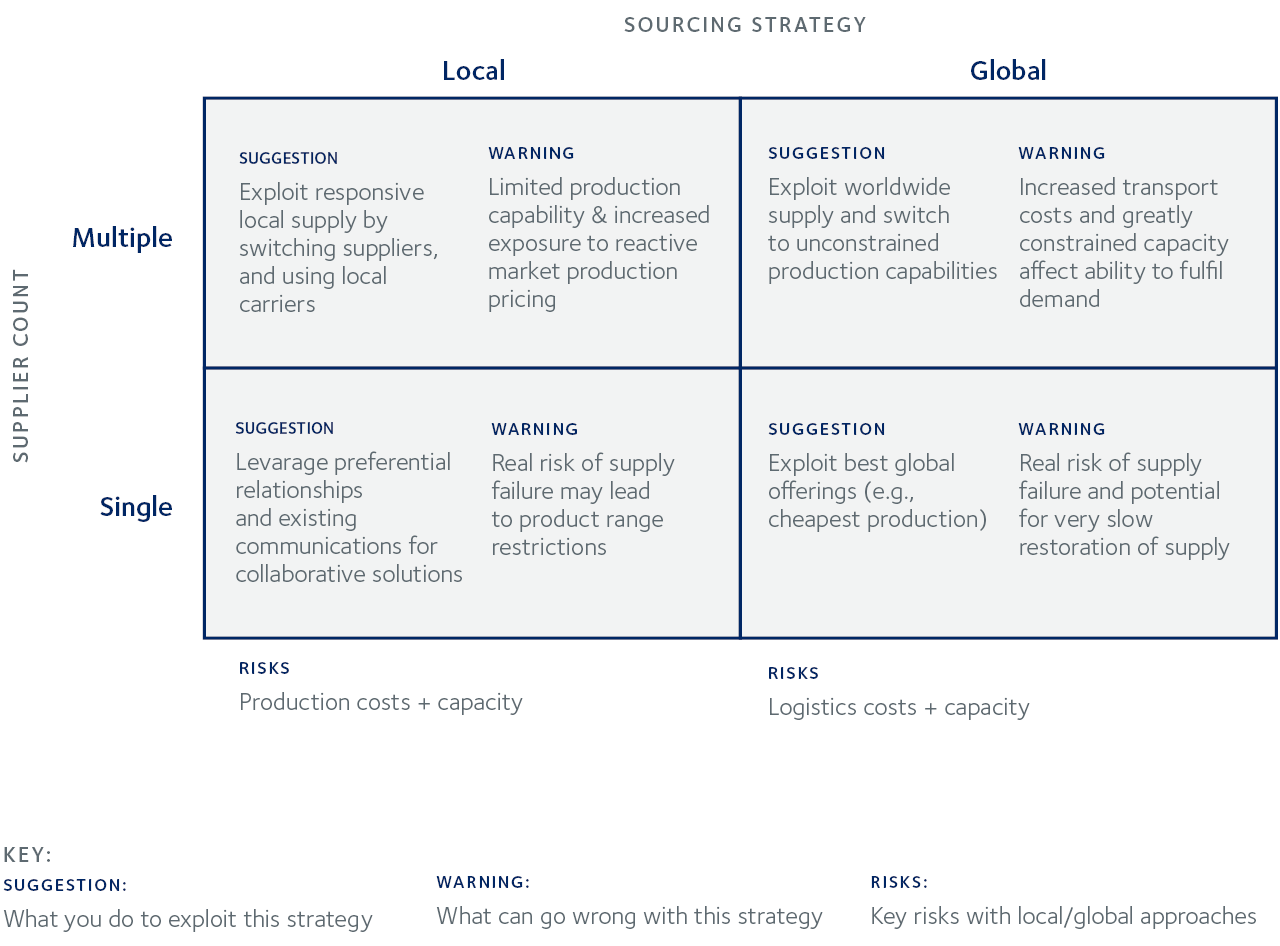
This matrix is a guide to supply chain and logistics professionals on what to look for and how to adapt their supply chain for the long term, considering the lessons learned from the COVID-19 response. In this sense, our recommendations are focused on mitigation and prevention and putting measures in place to ensure supply chains are resilient to any other future pandemics or major supply chain disruptions.
At one level, the disruptions experienced because of the pandemic are nothing new to organisations. They have always seen the inherent risks of single-source supply and balanced this against dual or multiple sourcing; the Thailand floods of 2011 brought geographic dispersion and the benefits and trade-offs with clusters of suppliers into focus; the 2011 earthquake and resulting tsunami in Japan completely disrupted automotive industry supply chain far beyond the automakers into tier-2, tier-3 and tier-4 suppliers. COVID-19 has in a way, brought many relevant elements together; single v multiple sourcing; geographical concentration of suppliers and looking at the entire supply chain versus just your tier-1 supplier.
The ability to design and implement new supply chains is not without constraints. Product redesign may also be required, and this takes time and investment. The resulting supply chain also still needs to be cost-effective or the organisation will not be there to face the next disaster. We have seen that some companies have recognised that the lines between manufacturing and logistics have changed and new supply chain services have been developed to bridge this gap. The respondents referred to the ability of their 3PL partners to work with them and this is one key takeaway in that the design of the new supply chain should not be constrained by how you perceive your current suppliers but also by what service they can and will be able to provide in the future. It is critical to cultivate and maintain a close partnership with key suppliers to enable timely and effective communication at all times. This is not something just for the crisis management phase.
A common theme from our interviews was that the organisations most able to recover were those who could look beyond the point problems of production, transportation, inventory, and demand to consider the whole supply chain with their service providers. Supply chain managers really should look at the entire supply chain. The traditional trade-off between production and transportation costs that underpins most local vs global evaluations views logistics as a cost only. The evaluation ignores the fact that the logistics provider can add value in creating a distributed network that incorporates the benefits of a globalised approach to production while also giving the ability to add resilience and responsiveness in local markets. Our research showed that those companies who had been able to work with their logistics partner(s) to set up a distributed network were better able to respond.
Supply chain managers cannot always redesign a product for a shorter supply chain. The product design or source of raw materials will always be a factor. However, when possible, companies can decouple parts of the supply chain to place inventory and product configuration activities close to the local market. This enables them to work with their supply chain partners in a way that mitigates the inherent risks of a long supply chain.
Based on the insights gained from this study, it seems that a supply chain-wide mitigation strategy is preferable to a company-specific one (and this agrees with previous findings in the supply chain disasters management literature; Altay and Ramirez, 2010). 3PLs are in an ideal position to coordinate such mitigation strategies as by definition they have a clear view of end-to-end supply chains.
Conclusion
The trend to localisation (regionalisation, local globalisation) and manufacturing closer to consumption was underway before COVID-19. However, the pandemic has only exposed the fragility of elongated supply chains. For some time, organisations have coped with major disruptions; tsunamis, flooding, volcanos, port strikes, etc., and even before the pandemic, the de-risking of supply chains to ensure continuity of supply was becoming increasingly important. Similarly, the recent development of trade tensions, such as the US-China conflict, the Brexit process, Japan-South Korea trade dispute, and other business dynamics towards deglobalisation (Hendry et al., 2019; Witt, 2019) are readily affecting and will continue to affect global supply chains (Lund et al., 2019). But it is the COVID-19 pandemic that has provided the catalyst for true change. The movement now for localisation (or blended strategies built upon it) seems to become greater, and de-risked, flexible and short supply chains have become increasingly attractive to firms, whilst governments see it as a way to stimulate economies and create jobs.
The initial stages of the pandemic led to supply chain shortages, not just of valuable medical and protective equipment but factories dependent upon inter-continental supply were subject to stoppages. There were surges in demand for e-commerce supply and bow-wave demand for consumer products such as home-based exercise equipment. Supply chains and continuity of supply moved high on organisational agendas and the topic of de-risking supply chains took on a more strategic nature. After the initial panic, a period of stabilisation and normality is taking place, but the question of de-risking has not gone away. The greater need for security, transparency and continuity of supply being enabled by advances in technology and communication is providing supply chain leaders with the ability not only to examine supply chains, but also to make decisions with the knowledge that the technology exists to initiate major supply chain transformations.
The pre-pandemic trends of national protectionism and the movement towards localisation was given more impetus during the pandemic as Governments see this as a way to stimulate and drive economic growth. On-going trade tariff restrictions and negotiations will still be an influential part of the future supply chain decision-making processes, as will the topic of sustainability. With increased legislation and consumer demands for more sustainable products with greater emphasis on product provenance, a greener supply chain, and the move to a circular economy.
Re-engineering the supply chain post-COVID-19 gives the opportunity of creating a more sustainable future-proof supply chain. Executives have been under pressure for some time to provide more sustainable solutions but balancing the cost of change against profits is a difficult balancing act and often immediate shareholder value has been prioritized. Now, the absolute need to re-evaluate supply chains and manufacturing strategies provides the opportunity to future proof the supply chain, and a major transformational overhaul allows the organisation to build in sustainability to a re-engineered structure. We recommend that supply chain and logistics managers now seek to reassess and recalibrate their supply chain in light of the insights gained from this research.
A note from the DSV authors of this report: DSV have developed a new supply calibration approach that allows supply chain and logistics managers to assess their supply chain against the wider business priorities and adapt their supply chain strategy and policies, manufacturing and supply chain decoupling points, logistics footprint and operational execution methods. Contact DSV to find out how to assess if your supply chain is calibrated or needs adapting for today’s new world.
References
Accenture (2020). Building Supply Chain Resilience: What to Do Now and Next During COVID-19. Available at https://www.accenture.com/us-en/about/company/coronavirus-supply-chain-impact
Altay, N. and Ramirez, A. (2010). Impact of Disasters on Firms in Different Sectors: Implications for Supply Chains. Journal of Supply Chain Management, 46, pp. 59-80.
Hendry, L.C., Stevenson, M., MacBryde, J., Ball, P., Sayed, M. and Liu, L. (2019). Local Food Supply Chain Resilience to Constitutional Change: The Brexit Effect. International Journal of Operations and Production Management, 39, pp. 429-453.
International Civil Aviation Organisation, ICAO (2020). Economic Impacts of COVID-19 on Civil Aviation. Available at: https://www.icao.int/sustainability/Pages/Economic-Impacts-of-COVID-19.aspx
Lund, S., Manyika, J., Woetzel, J., Bughin, J., Krishnan, M., Seong, J. and Muir, M. (2019). Globalization in Transition: The future of Trade and Value Chain. Report, New York: McKinsey Global Institute. Available at: https://www.mckinsey.com/featured-insights/innovation-and-growth/globalization-in-transition-the-future-of-trade-and-value-chains
Mitroff, I.I. and Alpaslan, M.C. (2003). Preparing for Evil. Harvard Business Review, 81, pp. 109-115.
Nikolopoulos, K. (2021). We Need to Talk about Intermittent Demand Forecasting. European Journal of Operational Research, 291, pp. 549-559.
Purvis, L., Spall, S., Naim, M. and Spiegler, V. (2016). Developing a Resilient Supply Chain Strategy During 'Boom' and 'Bust'. Production Planning and Control, 27, pp. 579-590.
Sodhi, M.S. (2016). Natural disasters, the Economy and Population Vulnerability as a Vicious Cycle with Exogenous Hazards. Journal of Operations Management, 45, pp. 101-113.
Spiegler, V.L.M, Naim, M.M. and Wikner, J. (2012). A Control Engineering Approach to the Assessment of Supply Chain Resilience. International Journal of Production Research, 50, pp. 6162-6187.
Wang, X. and Disney, S.M. (2015). The Bullwhip Effect: Progress, Trends and Directions. European Journal of Operational Research, 250, pp. 691-701.
Witt, M.A. (2019). De-Globalization: Theories, Predictions, and Opportunities for International Business Research. Journal of International Business Studies, 50, pp. 1053–1077.
World Health Organisation, WHO (2021). WHO Coronavirus Disease (COVID-19) Dashboard. Available at: https://COVID19.who.int
Zsidisin, G.A., Panelli, A. and Upton, R. (2000). Purchasing Organization Involvement in Risk Assessments, Contingency Plans, and Risk Management: An Exploratory Study. Supply Chain Management, 5, pp. 187.
Acknowledgements
-
The PARC Institute of Manufacturing, Logistics and Inventory resides within Cardiff Business School at Cardiff University and conducts leading research into forecasting and inventory planning, distributed manufacturing, 3D printing, and the shift towards a more sustainable circular economy. We work with a number of industry partners and are open to other companies interested in learning more about what we do.
Contact us for more info, follow our LinkedIn and Twitter page or visit www.cardiff.ac.uk/parc
-
DSV is a global supplier of transport and logistics services. With offices and facilities in more than 80 countries on six continents, we provide and run supply chain solutions for thousands of companies on a daily basis. Our reach is global, yet our presence is local and close to our customers.
For further information on DSV’s capabilities, visit www.dsv.com/uk.
Disclaimer
The research for this report was supported by Cardiff University, UK. The report is intended for general information only; it is based upon a review of the available literature together with primary research undertaken with organisations in Europe. Individuals or companies are advised to seek professional guidance regarding their specific needs and requirements prior to taking any actions resulting from anything contained in this report. Any such actions taken by individuals or companies are entirely at their own risk. Companies are also responsible for assuring themselves that they comply with all relevant laws and regulations, including those relating to intellectual property rights, data protection and competition laws or regulations. The images used in this document do not necessarily reflect the companies taking part in this research.
© April 2021, all rights reserved.
Any questions?
Our experts are ready to help. Get in touch and we'll find the solution you need.
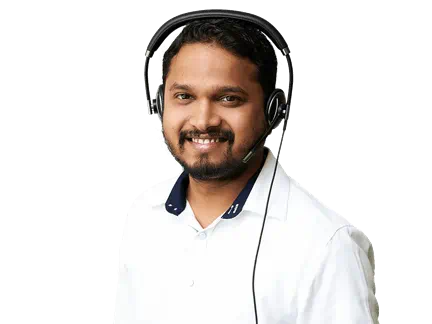