Flawless logistics
Volvo achieves top performance thanks to flawless logistics from DSV. The manufacturing and assembly process at Volvo Car Corporation in Ghent runs like a well-oiled machine, with thousands of component parts coming together to create one single car. For a timely and uninterrupted supply of components, Volvo relies on DSV Solutions. “We have an open and honest relationship in which we help each other without clinging to our official responsibilities,” says Michel Torreborre from Volvo Car Corporation.
One car a minute, 1,232 minutes a day: those are the impressive figures for Volvo Car Corporation in Ghent, Belgium, where 250,000 cars (XC60, S60, V40 and V40 Cross Country models) roll off the production line each year. To keep pace with such a tight schedule, day in day out, the supply of components has to be carefully managed too. To this end, Volvo receives support from DSV Solutions which opened a 50,000 square metre warehouse right next door to the Ghent factory in 2008.
Minimise tied-up working capital
The components are received and stored in the warehouse, from where they are delivered to the factory just-in-time and/or just-in-sequence. “We’ve been working with DSV since 2003. When we were faced with a lack of space in our factory in 2008, we outsourced a number of activities to DSV at the new facility,” explains Michel Torreborre, logistics manager at Volvo Car Corporation in Ghent. Volvo demands top performance from DSV. The car manufacturer only gives DSV between two and five hours’ notice, depending on the position along the assembly line, of which components are required and in which order. DSV delivers them to Volvo at one of three locations in the factory at least one hour before the components are to be assembled. “The entire process is designed to minimise the number of components lying around in the warehouse and in the factory, since they all represent tied-up working capital,” comments Michel Torreborre.
World-class level
Not only delivery time, but also delivery quality is extremely important. In order to avoid interruptions and delays to production, the companies have set the norm at a maximum of 30 picking errors per million picks. For the 550 DSV employees, that’s equivalent to just two mistakes each per year. “That is world-class level,” confirms Michel Torreborre. Both Volvo and DSV speak of an open and honest relationship in which teamwork is crucial. “Our collaboration is based on three pillars: operational excellence, innovation and cost management. Thanks to our open-book relationship, we can continually demonstrate that we’re working to further reduce costs and improve quality,” explains Miguel van Opbroeck, site manager automotive at DSV Solutions in Ghent. Torreborre agrees with him wholeheartedly: “DSV regularly suggests improvements that go above and beyond our contractual agreements. And in the case of any problems, there are no pointless discussions first – instead, we immediately set about finding solutions together. This is definitely the right way forward.”
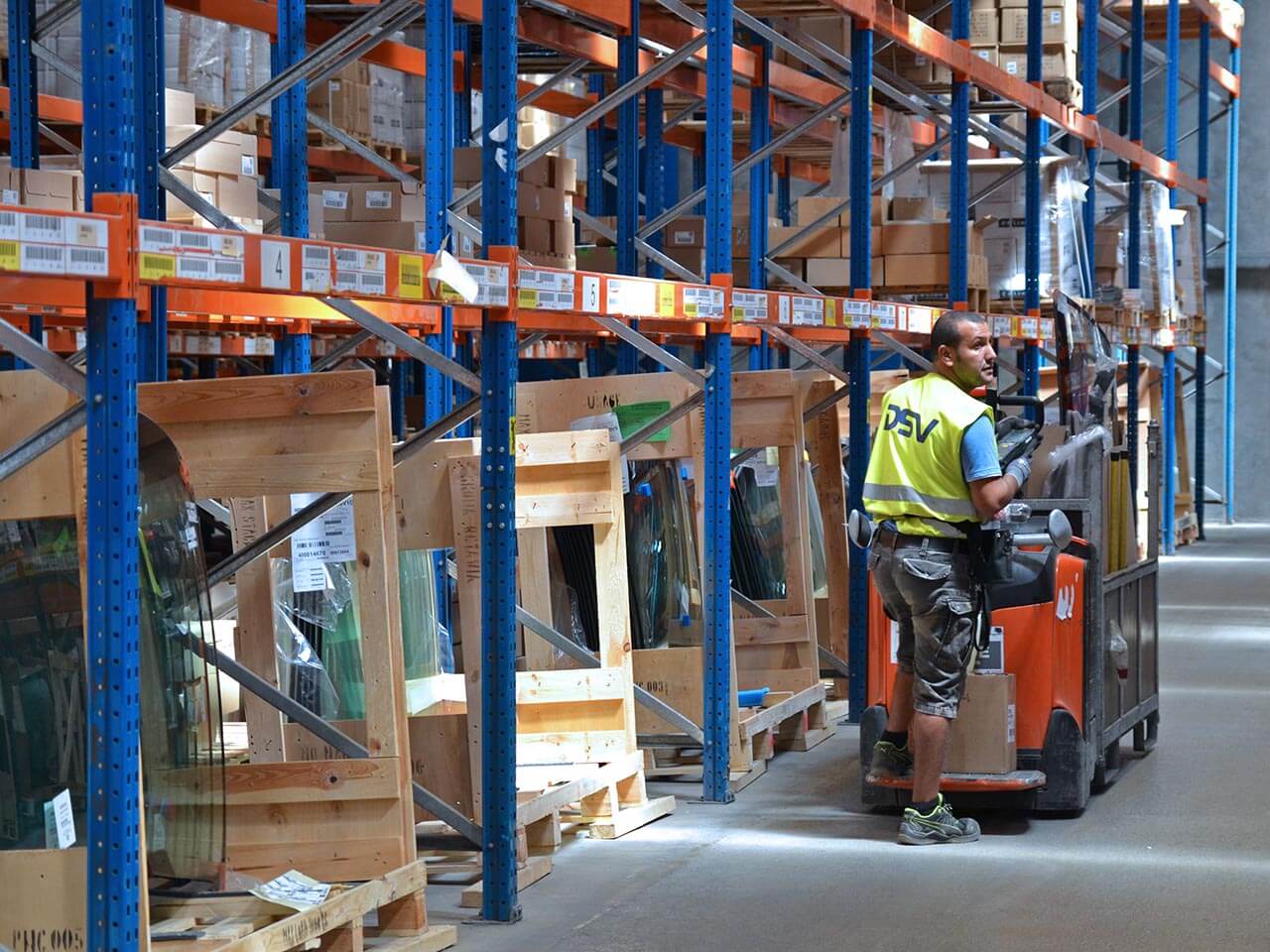
Any questions?
Our experts are ready to help. Get in touch and we'll find the solution you need.
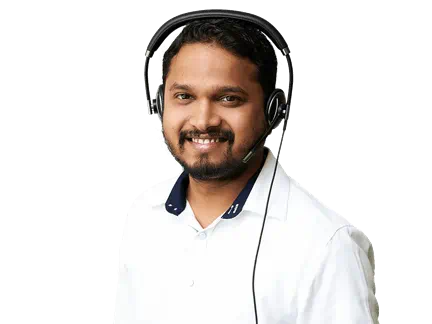