Optimierung der Lieferkette in der Automobilindustrie
Kosteneinsparungen in der Wareneingangslogistik der Automobilindustrie – nur Verhandlungssache?
Die Reduzierung der Lieferkettenkosten beginnt fast immer mit dem Wunsch, Verträge mit Logistikdienstleistern neu auszuhandeln. In der nächsten Phase werden Ausschreibungen durchgeführt, um die Preise zwischen den Lieferanten zu vergleichen.
Diese Strategie kann kurzfristig Vorteile bringen, aber es gibt Grenzen, welche Einsparungen erzielt werden können, wenn mittel- bis langfristig Druck auf die Lieferanten ausgeübt wird.
Die Süße einer anfänglichen Kostenreduzierung kann schnell sauer werden, sobald die Kosten außerhalb der Kontrolle des Lieferanten oder Ihrer Kontrolle steigen und einen bitteren Nachgeschmack hinterlassen. Solche Erhöhungen können Kraftstoffkosten beinhalten, aus Ungleichgewichten der Marktkapazität resultieren oder einfach auf eine erhöhte Komplexität Ihrer Logistik zurückzuführen sein.
Nur wenige würden nicht zustimmen, dass Optimierung der Weg in die Zukunft ist - aber was ist der optimale Weg zur Optimierung?
Tier 1 ist bereits überwiegend optimiert
OEMs - Original Equipment Manufacturers: Die Unternehmen, deren Name auf den fertigen Fahrzeugen steht, sind sehr geschickt darin, die Inbound-Logistik zu optimieren. In den meisten Fällen veranlasst der OEM den Versand vom Komponentenwerk (als Tier 1-Lieferant bezeichnet) zum Fahrzeugmontagewerk.
Dies hat dazu geführt, dass Tier-1-Lieferanten ihre Fabriken in der Nähe der Montagewerke aufstellen, sodass Komponenten für die Just-in-Time-Fertigung fast direkt an die Montagelinie geliefert werden können. Viele dieser Komponenten sind relativ groß und schwer zu lagern, so dass es viel einfacher ist, sie je nach Bedarf herzustellen, als dass sie Lagerfläche mit daraus resultierenden zusätzlichen Logistikbewegungen in Anspruch nehmen.
Wenn es um Lieferanten der Tier 1-Fabrik geht (bekannt als Tier 2-Lieferanten), ist es weitaus wahrscheinlicher, dass diese Lieferanten an einem anderen Ort angesiedelt sind - sogar in einem anderen Land. Die Transportkosten und die Logistik für den Tier-2 --> Tier-1-Teil der Lieferkette sind daher komplexer.
Transport Intelligence Report
Im Jahr 2014 veröffentlichte Transport Intelligence einen Bericht über Automobillogistik, der auf der Arbeit des International Car Distribution Programme (ICDP) basiert. In dem Bericht wurden drei Kategorien von Logistikkosten ermittelt und die Ausgaben aller europäischen Automobilhersteller aufgeführt:
- Inbound zur Fertigung für Autohersteller (OEMs): Ausgaben für die Logistik zum und innerhalb des Montagewerks des OEMs. Bei dieser Aktivität werden in der Regel Waren von Lieferanten auf unterschiedliche Weise abgeholt.
- Inbound zur Fertigung für Zulieferer der Automobilhersteller (Tier1/Tier2): Logistik von Materialien in und um alle Einrichtungen der Lieferanten (dies sind versteckte Kosten für die OEMs, die im Preis der Komponenten enthalten sind).
- Fertiges Fahrzeug / Outbound: Fertigfahrzeuge der Fahrzeughersteller, einschließlich Transport, Handhabung / Inspektion vor der Auslieferung (PDI) und Bestandsverwaltung. Der Aftermarket umfasst den Vertrieb von Ersatzteilen.
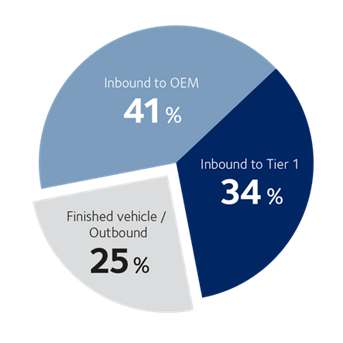
Die Zahlen zeigen, dass die Kosten für Inbound to OEM und Inbound to Tier 1/2 Logistik zusammen 75% der gesamten Logistikkosten ergeben.
Es ist daher ratsam, die Einsparungen zu betrachten, die in diesen Kategorien zusammen erzielt werden können.
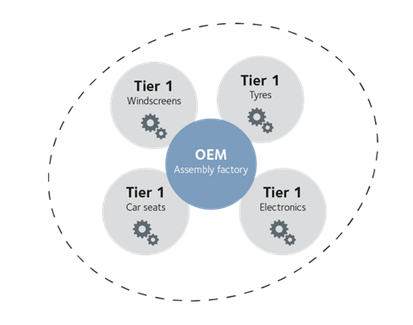
Erweiterung der Optimierung auf Tier 2
Um dies zu veranschaulichen, betrachten wir eine der vielen Arten von Artikeln, die von einem Tier-1-Zulieferer an einen OEM geliefert wurden - Autositze.
Der Autositzlieferant wird beauftragt, Sitze an das Montagewerk des OEM zu liefern.
Wie andere Zulieferer befindet sich das Werk sehr nahe am Montagewerk des OEM, und zwar so nahe, dass es sich häufig innerhalb derselben Verbindung befindet, sodass der Transport zwischen den Produktionslinien wahrscheinlich mit Gabelstaplern erreicht werden kann.
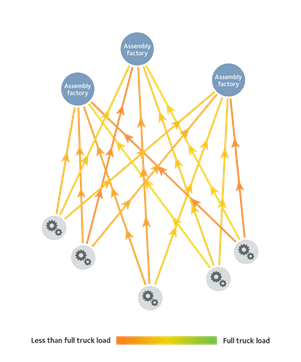
Leder
Es ist unmöglich, dass alle Fabriken in einer Lieferkette nahe beieinander liegen - insbesondere wenn man Rohstoffe berücksichtigt, die aus der Landwirtschaft oder sogar aus dem Meeresboden stammen können, wenn Öl zur Herstellung von Kunststoffen verwendet wird. Beispielsweise wird Aluminium durch energieintensives Schmelzen hergestellt, das in der Nähe einer zuverlässigen, billigen Energieversorgung erfolgen muss.
Eines der Materialien für die Herstellung von Autositzen ist Leder.
Jeder Lederlieferant beliefert tatsächlich mehr als eine Autositzfabrik und mit ziemlicher Sicherheit mehr als einen OEM - das untenstehende Diagramm zeigt diese Ströme in vereinfachter Form und die Tatsache, dass nicht jede Lieferung eine volle Lkw-Ladung ist. Jeder Lieferant hat daher mehrere Lkws pro Woche, die Teilladungen (LTL - „weniger als volle Lkw-Ladungen“) sammeln und zu jeder von ihnen gelieferten Fabrik fahren.
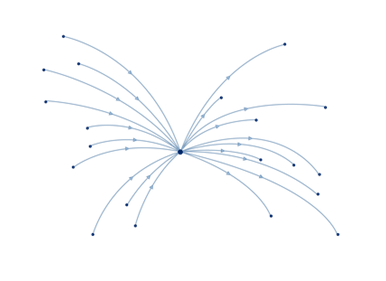
Analog zum Hub-and-Spoke-Airline-Modell:
Wenn Sie von einem großen Flughafen zum anderen fliegen möchten, haben Sie wahrscheinlich die Wahl zwischen Direktflügen ohne Zwischenlandung.
Aber wenn die Nachfrage nach Sitzplätzen zwischen kleinen Städten nicht ausreicht, ist es wahrscheinlich, dass Sie eine Verbindung über einen Drehkreuzflughafen nehmen müssen.
Da es nicht möglich ist, ein ganzes Flugzeug mehrmals täglich auf einer direkten Route zu füllen, kann eine Fluggesellschaft einen effizienteren Betrieb durchführen, indem sie größere Flugzeuge von den kleinen Städten zu einem großen Hub-Flughafen fliegt. Am Hub steigen die Passagiere in andere Flugzeuge um, die sie an ihren endgültigen Bestimmungsort bringen.
Genau dieses Hub-and-Spoke-Modell kann angewendet werden, um eine Lieferkette zu optimieren.
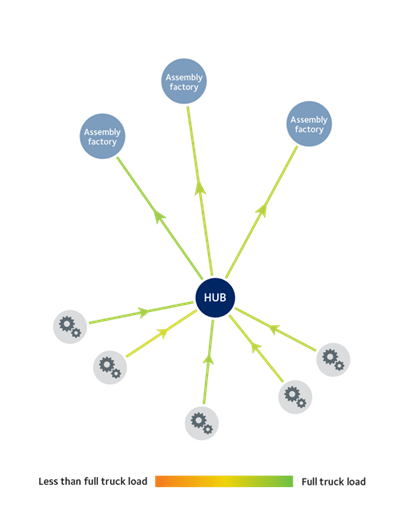
Vertriebszentrum
Durch die Aufstellung eines Distributionszentrums an einem geeigneten Ort kann die Lieferkette wesentlich effizienter werden, indem die weniger als vollen Lkw-Ladungen und die direkten Nonstop-Sendungen reduziert werden. Diese Konsolidierung und Neuausrichtung der Warenströme reduziert die Anzahl der benötigten Lkws. Darüber hinaus kann das Verteilungszentrum ein Cross-Dock sein, wenn Ein- und Ausgang besonders gut koordiniert werden können und so Lagerung vermieden wird.
Das Ergebnis sind erhebliche Einsparungen. Es ist auch viel einfacher, Just-in-Time-Lieferungen zu koordinieren. Natürlich ist die geografische Lage des Distributionszentrums wichtig, um keine unnötig langen Transitzeiten zu haben. Ein Distributionszentrum in der Kette verlängert zwar die gesamten Transitzeiten, dies ist jedoch kein Problem, sobald die Kette läuft und die Transitzeiten in die Just-in-Time-Planung einbezogen werden. Die Lieferkette ist dadurch einfacher und effizienter.
Milkruns
Diese Methode zur Optimierung in einem Distributionszentrum muss nicht allein stehen. Sie kann natürlich auch mit anderen Methoden wie dem sogenannten Milkrun kombiniert werden.
Der Milkrun optimiert die lokale Sammlung und ist nach den Milchtankern benannt, die mehrere Milchviehbetriebe besuchen, um Milch zu sammeln. Sie kehren erst dann zum Depot zurück, wenn der Tanker voll ist oder keine Milch mehr in der Gegend zum Sammeln vorhanden ist.
Diese Art der Optimierung bringt viele Vorteile: Durch den Versand von mehr vollen Lkw-Ladungen und weniger Teilladungen ist die Anzahl der Lkw-Bewegungen geringer, was zu einer effizienteren Nutzung der Dockkapazität, der Lkw und Fahrer, des Kraftstoffs, der Mautgebühren und vieler anderer Aspekte führt - nicht zuletzt zu einer Verringerung der CO2-Emissionen.
Schlussfolgerungen
Indem nicht nur die Teile der Automobilzulieferkette untersucht werden, die an die Endmontagestufe (Tier 1) angrenzen, können umfangreiche Transport- und Logistikeinsparungen erzielt werden. Die Transportkosten für den eingehenden Transport zu Tier 1 und Tier 2 sind dreimal höher als für den ausgehenden Transport von der Endmontage zu den Endkunden.
Ein Großteil der Kosten für Komponenten in niedrigeren Lieferkettenebenen beinhaltet versteckte Kosten, die darauf zurückzuführen sind, dass Lieferketten nicht optimiert werden.
Eine sorgfältige Analyse von mehr als nur der obersten Ebene der Lieferkette kann zu erheblichen Einsparungen führen, indem der Ladeverlust reduziert wird, der durch den Versand zu vieler Teilladungen anstelle von Vollladungen entsteht.
Über den Autor
Ronald Poort ist Chief Commercial Officer DSV Contract Logistics.
Haben Sie Fragen?
Unsere Experten helfen Ihnen gerne weiter. Kontaktieren Sie uns und wir finden die passende Lösung für Sie.
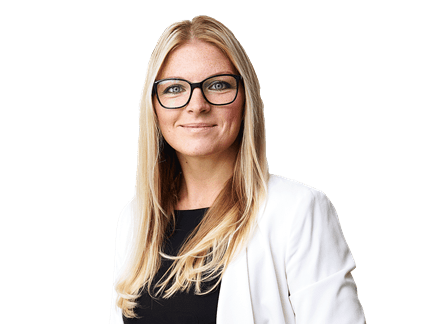