DSV Wins Platinum, Bronze and Two Enviro Awards At Logistics Achiever Awards 2018
Waste solution winning streak going
Photo: Brett Sauerman, General Manager - DSV, Abdul Abrahams, Branch Manager - DSV, Billy Tshabalala, Business Owner – Basadi Recyling, Fikelwa Makhanda, Business Owner – Basadi Recyling, André Hough, Operations Director - DSV, Jacques du Plessis, Logistics Engineer - DSV and Greg Saffy, Managing Director - DSV, with four awards at the LAA
DSV South Africa won a Platinum, a Bronze and two Enviro awards at the Logistics Achiever Awards 2018.
DSV’s innovative waste solution at the DSV Automotive Supplier Park in Rosslyn, Pretoria, won the Bronze award. Following the three DSV Gold awards in 2017. This entries also won Enviro awards.
The Logistics Achiever Awards recognise professionalism and excellence in the effective application of strategic, tactical, and operational logistics and supply chain management principles, concepts, and practices in Southern Africa.
DSV CEO Keith Pienaar said the awards reflected DSV’s innovative, customer-centric approach to developing new services, and its deep commitment to job creation and protecting the environment. “Importantly, we are able to turn challenges into opportunities and then deliver significant economic and efficiency outcomes for our customers and the broader communities in which we live and work”, he said.
Basadi Recycling and the opportunity in waste
Apart from solving a growing waste problem at DSV Automotive’s purpose built, 38,000m2 aftermarket fulfilment facility in Pretoria, the waste solution has had the added benefits of supporting previously disadvantaged individuals into a new business venture and enhancing the company’s support for needy communities.
The fulfilment facility opened in 2007, and houses approximately 108,200 unique part numbers. The facility processes on average 17 inbound containers across all operations and ships approximately 4,500 order lines every day to over 200 dealers across South Africa and the BLNS countries.
But the success of the facility created challenges, not least with the waste generated by activities increasing by 300% between 2010 and 2016. Space constraints and compliance risks were compounded by the complexity of managing additional waste streams over time. “We recognised that waste management was not a core competency and as a result the waste streams were poorly managed and was posing a risk to both ourselves and our customers”, said Andre Hough, DSV Operations Director.
In addition, there has been little collaboration across operations over the years, resulting in the appointment of multiple providers. But the growing problems and increasing environmental awareness emphasised the need to make a change. “Once we had analysed the nature of the waste – cardboard made up 30% of the waste, crates accounted for 20%, while general waste, pallets and metal each accounted for 10% - we were better placed to develop solutions in terms of an Enterprise Development Initiative”, he said.
The appointment of a single provider to manage the waste streams was a logical move, and became more meaningful when Basadi Recyclying was established and registered with the Department of Trade and Industry – with a black male (49%) and black female (51%) shareholding. Procedural controls were put in place and the company’s performance would be managed through a Service Level Agreement.
The results have exceeded expectations: the supplier development programme has enabled both entrepreneurs to better understand and manage their business in a sound way, revenue has increased by 60% since inception and two general workers have been employed within the supplier park.
The broader community has also benefited through job creation (to use waste wood to build Wendy houses for less fortunate people at reasonable prices) and support of community organisations, including the Temogo Day Care Centre and Lebogang Creche.
Any questions?
Our experts are ready to help. Get in touch and we'll find the solution you need.
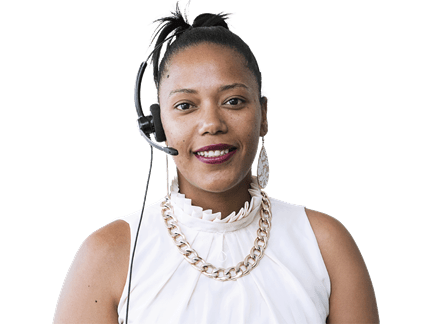