Removing the need for physical inventory and extending product life cycle
This expert opinion takes a closer look at how additive manufacturing and 3D printing can overcome some of the complexities involved with spare parts – and how spare parts on demand is becoming a viable option for businesses in many different industries.
One company that is exploring the potential of additive manufacturing is Glory. They have been working with RemakerSpace, part of the PARC Institute run by Cardiff University and DSV, to explore how they can use 3D printing of spare parts in their business.
The challenges of spare parts
Firstly, they are a crucial part of a product’s lifecycle and, secondly, they cover a variety of situations. In the case of breakdown repairs, spare parts need to be available at short notice, ideally located close by. However, if the parts are needed for preventative maintenance, they are not as urgent or business critical. This places different demands on the way they are produced and stored.
If we consider a conventional spare parts network, parts are typically manufactured using techniques such as casting, forging or moulding – and then shipped to their destination. Here they are stored in a warehouse until they are needed or until they’ve passed their useful life or become obsolete.
Anyone involved in the production, transport or storage of spare parts will agree that this involves a degree of waste. There is the cost of manufacturing parts that may not be used, transportation of parts to places they might not be needed, and the cost of storing products that run the risk of becoming obsolete.
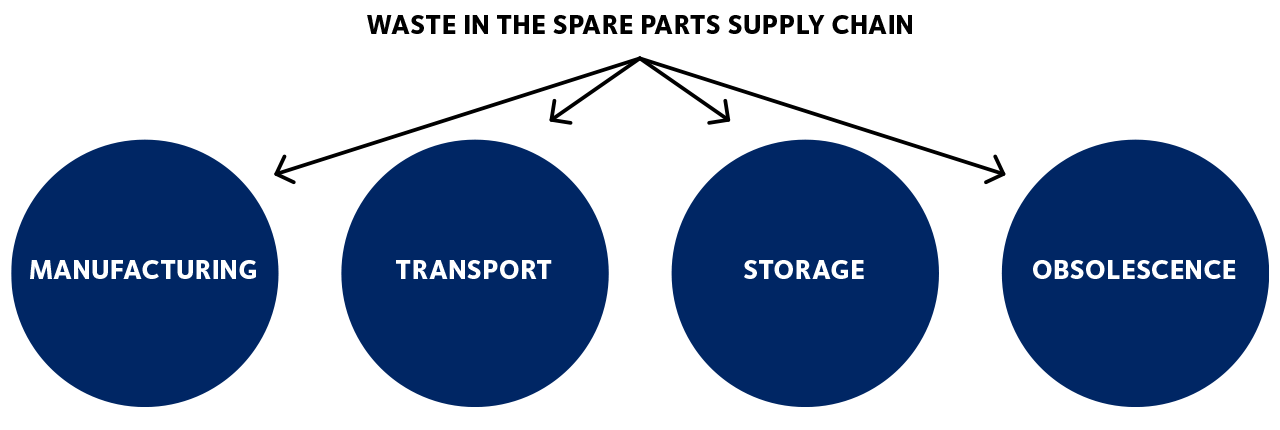
When is the “last time buy”?
At the end of a product lifespan, companies are forced to rely on a “last time buy”. This is the final purchased quantity of spare parts to support the operation of the equipment or product for the remainder of its lifetime. Making this decision is notoriously difficult. Buy too many parts and you might be left with an expensive and obsolete stock. Buy too few and risk not being able to repair your product and being forced to invest in a costly new replacement.This is where additive manufacturing and spare parts on demand (SPoD ) can change the way we consider spare parts. Instead of maintaining a costly physical inventory of spare parts, it is now increasingly possible to have a digital inventory of design files that can be accessed when needed to create spare parts on demand. This can prevent much of the waste inherent in the production and transportation of spare parts and avoid the need to make that difficult “last time buy” decision.
How additive manufacturing transforms the supply chain
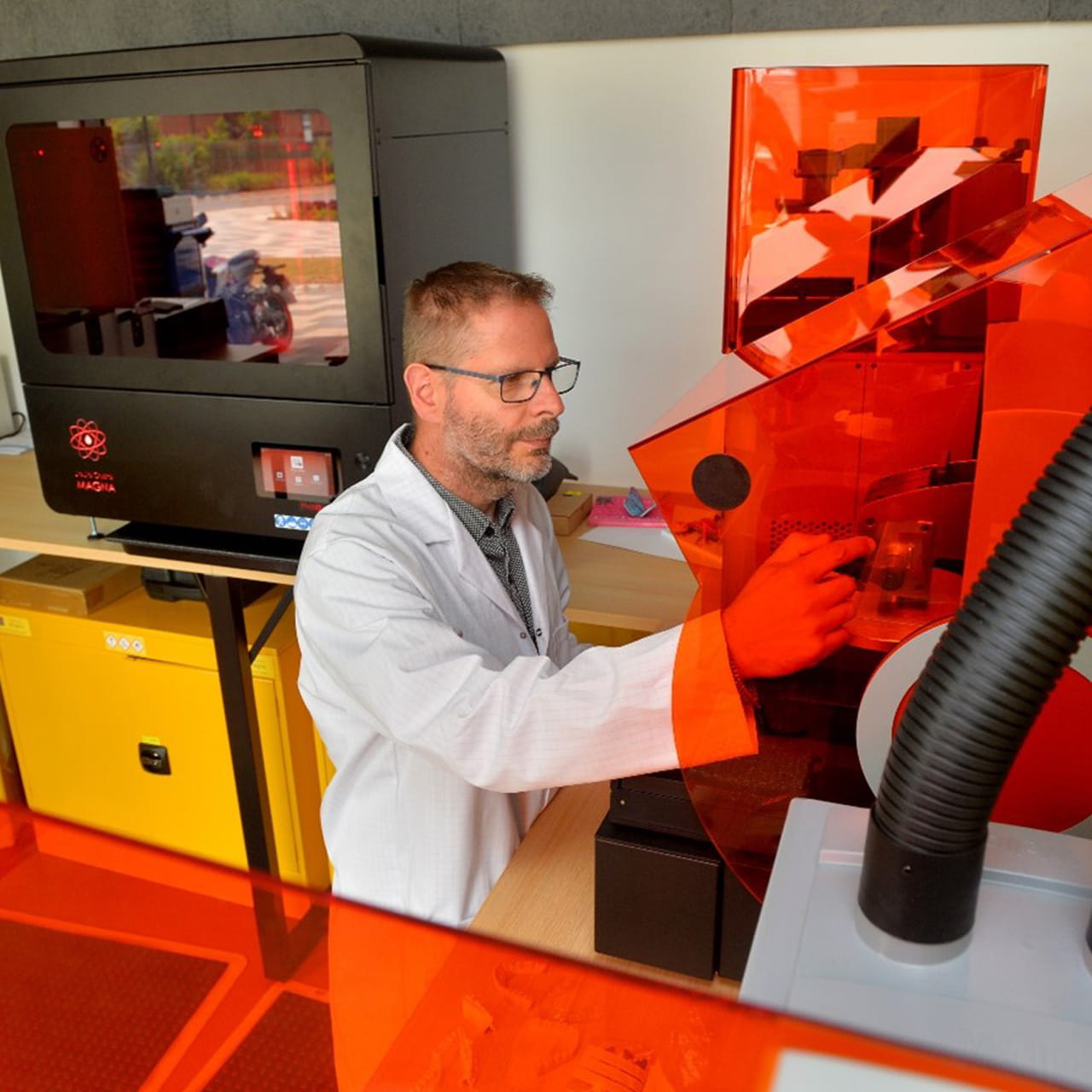
So what is additive manufacturing?
In short, it refers to the process of building a new part one layer at a time. This is the opposite of subtractive manufacturing, where a part is created out of a solid block of material. 3D printing – the process of creating objects in layers – is an example of additive manufacturing.
In other words, the potential of 3D printing is now available and used by many more manufacturers and industries, including the aerospace and medical industries. In particular, 3D printing can be a good fit for industries with long-lasting machinery, where support via traditional manufacturing is difficult due to the low quantity of parts required.
Benefits of 3D printing spare parts
-
Enable local manufacturing and reduce transport time
-
Reduce waste as only the parts needed are produced
-
Increase speed as parts can be made quickly
Case: The switch to spare parts on demand
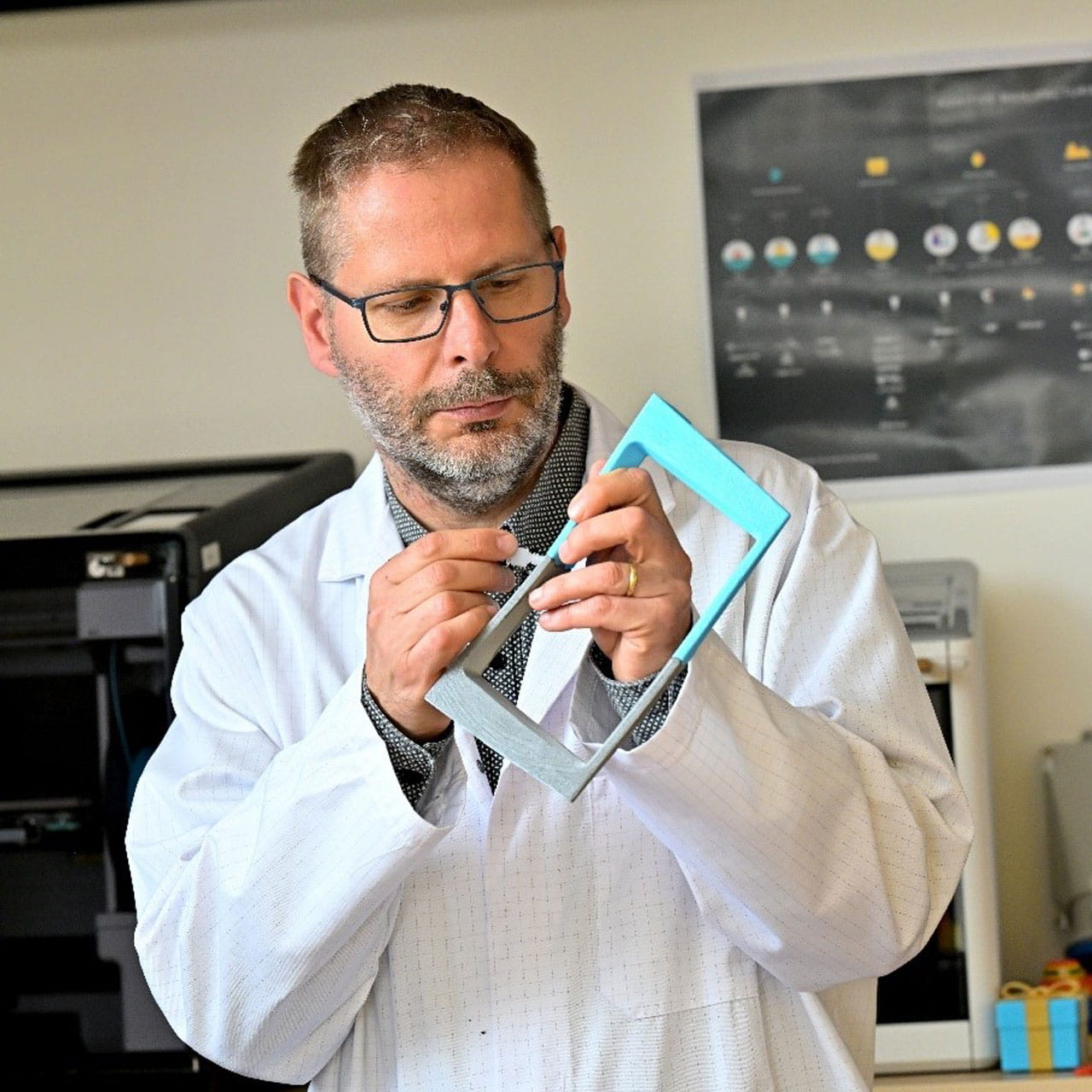
Working with cash, Glory cannot afford anything but the highest quality components and need to ensure part availability to keep their machines and systems running smoothly. RemakerSpace is helping Glory identify materials, components and processes that can help them realize the benefits of additive manufacturing for their low volume production parts.
This collaboration has shown that by switching to spare parts on demand where possible, Glory can potentially reduce physical stock, shorten lead times and cut tooling costs.
What’s needed for additive manufacturing?
Before deciding to invest in 3D printing of parts, a careful assessment of spare part inventories, including technical and economic factors, such a materials size and shape, demand frequency and predictability, needs to be made.
Part design needs to factor in the considerations and limitations of 3D printing. This means avoiding thin features or large overhangs that are difficult to create using 3D printers. Once a successful design has been developed, it needs to be created as a digital file and stored in a digital inventory. Then, when a spare part is needed, the design can be accessed and an order placed with a production partner who creates the part using 3D printing.
The process to making spare parts printable
- Consider the design of the parts in terms of what is possible using 3D printing
- Set up a digital inventory with designs of all parts and components
For Glory, working with RemakerSpace has supported their circularity goals by helping them explore the positive implications of spare parts on demand with operationalised suggestions and insights.
“Our association with RemakerSpace has significantly improved our understanding of the circular economy and particularly 3D printing as a potential and realistic option for production parts. Reduced global footprint and improved efficiencies with local manufacture will help reduce our impact on the planet and benefit our customers with express delivery of selected parts.”
About RemakerSpace
RemakerSpace is a Cardiff Business School and PARC Institute not-for-profit initiative that is funded by the Welsh Government, and operates with support from DSV. The centre is dedicated to enabling the circular economy and ending planned obsolescence by extending the life cycle of products. They undertake world-class research and bridge the gap between theory and practice for the benefit of a more sustainable economy, environment and society.
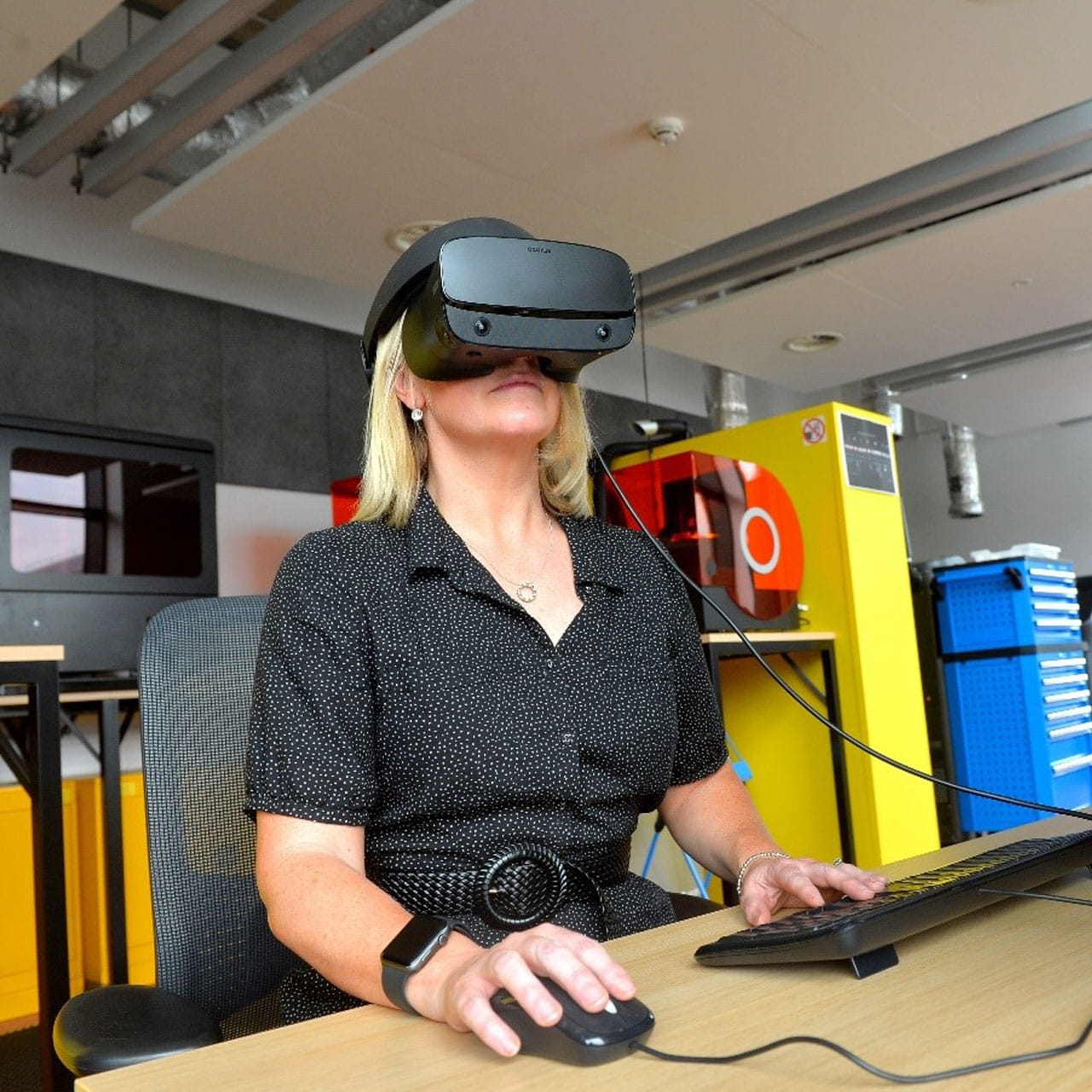
About the experts
Aris Syntetos is Distinguished Research Professor of Decision Science and the DSV Chair of Manufacturing and Logistics at Cardiff Business School, Cardiff University.
Dave Watson is Director, Logistics Manufacturing Services (LMS) Commercial, at DSV.
Mike Wilson is Executive Vice President LATAM, Logistics Manufacturing Services, and Inventory Management Solutions at DSV, and Honorary Visiting Professor at Cardiff Business School.
Any questions?
Our experts are ready to help you setting up the right logistics solutions utilizing 3D printing. Get in touch and we'll find the solution you need.
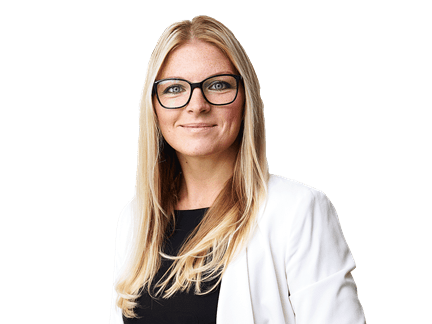