GDP-certified for the safe handling, storage and distribution of drugs
Many pharmaceutical companies require that Panalpina's business units that handle their products are certified according to Good Distribution Practice (GDP), a set of guidelines for the proper distribution of medicinal products for human use. Today, 70 Panalpina business units around the world are GDP-compliant. Out of these locations, 30 are GDP-certified and this number is on the increase.
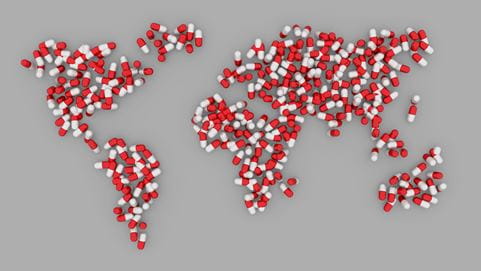
Panalpina realizes that maintaining product quality and safety of pharmaceuticals in the supply chain is highly critical. In line with this, the company has taken strong initiatives to exceed the expectations of healthcare customers.
Many pharmaceutical companies require that business units that handle their products are certified according to Good Distribution Practice (GDP), a set of guidelines for the proper distribution of medicinal products for human use. Today, 70 Panalpina business units around the world are GDP-compliant. Out of these locations, 30 are GDP-certified and this number is on the increase. The GDP quality assurance standard includes stringent requirements for the handling, storage and distribution of pharmaceuticals.
“With increasingly global supply chains and the emergence of high-value products, there is a heightened demand for strict quality and temperature control measures to ensure the safety and integrity of pharmaceutical products throughout long-distance deliveries,” explains Andreas Sahli, Panalpina’s global head of industry vertical healthcare. “Stakeholders across the supply chain can rely on us to deliver GDP-compliant transport, storage and distribution solutions worldwide.”
Panalpina holds thousands of trainings on GDP topics each year and around 3,000 employees are currently GDP-qualified. In 2018, Panalpina will roll out its own GDP training materials, and continue its program to qualify its staff, thus expanding its capabilities and knowledge in this regard.
Central to Panalpina’s success in quality management is its self-assessment process. The company’s quality, health, safety and environment (QHSE) team performs 40-50 GDP audits per year to look for opportunities for improvements in established processes and standards and to identify any systemic issues that require addressing. “When a non-conformance is identified, a root-cause analysis is performed immediately to identify the origin of the issue, and a corrective action plan is developed,” says Lindsay Zingg, global head of QHSE at Panalpina.
Systematic subcontractor management
As an asset light organization, Panalpina is critically dependent on the performance of its subcontractors and their adherence to agreed processes and procedures. As part of its environmental, quality and safety management systems, Panalpina also has a rigorous program of subcontractor audits, whereby the working standards and corporate controls of subcontractors are assessed regularly. These audits include environmental performance standards, and adherence to labor and human rights performance. In 2017, 266 subcontractor audits were performed.
Panalpina is using Validaide, a new online platform it has co-developed, to qualify its key suppliers and make lane-risk assessments, especially for the healthcare industry. On the open platform, customers and suppliers of services are connected to standardize and improve supplier qualification for different product categories and transport modalities. In 2018, Validaide will be further rolled out to continue to leverage the advantages the system offers.